Allen Bradley is a brand name for a line of automation and control products manufactured by the Rockwell Automation company. These products include programmable logic controllers (PLCs), human-machine interfaces (HMIs), industrial control components, sensors, and software for industrial automation.
Allen Bradley products are used in a wide range of industries including automotive, food and beverage, packaging, energy, and more. They are designed to improve productivity, reduce downtime, and ensure quality and safety in manufacturing and industrial processes.
Some of the key features of Allen Bradley products include flexibility, scalability, and compatibility with a variety of communication protocols. The products are also known for their ruggedness and reliability, making them a popular choice for industrial applications in harsh environments.
Many Allen Bradley machines and equipment use batteries for various purposes. For example, some programmable logic controllers (PLCs) and human-machine interfaces (HMIs) may use batteries to retain memory and preserve data in case of power outages or shutdowns. These batteries are typically small, replaceable, and located on the circuit boards inside the devices.
In addition to PLCs and HMIs, other Allen Bradley machines and equipment that may use batteries include barcode scanners, handheld terminals, wireless access points, and other wireless communication devices.
It’s worth noting that the specific types of batteries used in Allen Bradley machines and equipment can vary depending on the device and its intended application. Some devices may use standard AA or AAA batteries, while others may require specialized lithium-ion or nickel-metal hydride batteries. If you have a specific Allen Bradley device in mind, it’s best to refer to the product documentation or contact the manufacturer for more information on battery requirements.
The Allen Bradley SLC-500 is a series of programmable logic controllers (PLCs) manufactured by Rockwell Automation under the Allen Bradley brand. The SLC-500 series was first introduced in 1986 and is still in use today, although it has been largely superseded by newer models.
The SLC-500 PLCs are designed for a wide range of industrial control applications, including process control, discrete control, and motion control. They are known for their reliability, flexibility, and ease of use.
Some key features of the SLC-500 series include:
Modular design: The SLC-500 PLCs are modular, which means they can be customized to meet the specific needs of an application. Users can add or remove input/output (I/O) modules as needed to control different types of equipment.
Programming: The SLC-500 PLCs are programmed using the RSLogix 500 software, which uses ladder logic or other programming languages to create logic functions. The software is user-friendly and offers a variety of programming tools and functions.
Communication: The SLC-500 PLCs support a range of communication protocols, including Ethernet/IP, DeviceNet, ControlNet, and others. This allows for easy integration with other equipment and systems.
Redundancy: The SLC-500 series offers redundant controllers and I/O modules for increased reliability and safety.
The Allen Bradley SLC-500 programmable logic controllers (PLCs) use a battery to retain the data in the controller’s memory during a power outage or when the unit is shut down. The battery is a lithium or alkaline 3V 1000mAh battery.
The battery in an SLC-500 PLC is located on the processor module. To replace the battery, you need to power down the unit, remove the cover of the processor module, and locate the battery holder. You can then remove the old battery and insert the new one, making sure to orient it correctly.
It’s important to replace the SLC-500 battery on a regular basis to avoid losing data and to ensure the reliable operation of the PLC. The recommended replacement interval for the battery varies depending on the application and usage of the PLC, but a typical interval is between 2 and 5 years. You can check the battery status and health using the RSLogix 500 software or the processor module’s display.
Note that when replacing the battery, you should follow appropriate safety procedures to avoid electric shock or damage to the equipment. It’s also important to dispose of the old battery properly according to local regulations.
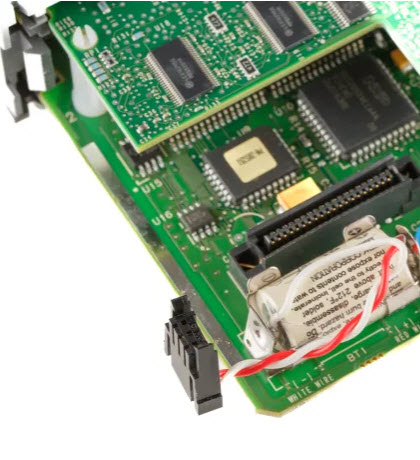
Leave a Reply